Innovation and Technology in Indian Valve Manufacturing Sector
- Aira Euro Automation
- Jun 6, 2023
- 12 min read
In recent years, the Indian valve manufacturing sector has witnessed remarkable technological advancements that have revolutionized the industry. These advancements have not only enhanced the efficiency and performance of valve manufacturing processes but have also positioned India as a global player in the valve manufacturing market. Here are some key technological advancements that have transformed the Indian valve manufacturing landscape:
Automated Manufacturing: Automation has played a significant role in streamlining valve manufacturing processes in India. Automated machinery and robotics have replaced traditional manual labour, resulting in improved precision, productivity, and quality control. Automation has also reduced human errors and increased production speed, thereby reducing manufacturing costs.
Digitalization and IoT Integration: Indian valve manufacturers have embraced digitalization and the integration of Internet of Things (IoT) technologies. This has enabled real-time monitoring of valve performance, predictive maintenance, and remote access to valve data. IoT integration has facilitated data-driven decision-making, optimized maintenance schedules, and minimized downtime.
Advanced Materials and Manufacturing Techniques: Indian valve manufacturers are increasingly adopting advanced materials and manufacturing techniques. The use of high-quality alloys, polymers, and composites has improved the durability and resistance of valves to extreme conditions, corrosion, and wear. Advanced manufacturing techniques, such as 3D printing and additive manufacturing, have revolutionized the prototyping and production processes, allowing for complex designs and customization.
Smart Valve Technology: Indian valve manufacturers are developing smart valves equipped with sensors, actuators, and communication capabilities. These smart valves can monitor and regulate flow, pressure, and temperature autonomously, leading to enhanced process control and optimization. Smart valves also enable remote monitoring and control, enabling operators to make real-time adjustments and respond to changing conditions promptly.
The technological advancements in Indian valve manufacturing have significantly contributed to the growth and competitiveness of valve manufacturers in India. These advancements have not only improved the domestic market but have also positioned Indian valve manufacturers as reliable and technologically advanced suppliers in the global market. Valves Manufacturers in India have leveraged these technological advancements to cater to a wide range of industries, including oil and gas, power generation, chemical, water treatment, and more. With continuous research and development, collaboration, and innovation, the Indian valve manufacturing sector is poised for further technological advancements in the coming years, reinforcing its position as a game changer in the industry.
Automation and Robotics: Revolutionizing the Indian Valve Manufacturing Sector
Valves Manufacturers in India are experiencing a significant transformation in their operations with the advent of automation and robotics. This technological revolution is reshaping the entire valve manufacturing process, bringing numerous benefits and enhancing efficiency and productivity.
Automation has enabled Indian valve manufacturers to streamline their production lines, minimizing human errors and increasing overall accuracy. Automated systems can handle repetitive tasks with precision, resulting in improved quality control and reduced defects.
Robotics plays a pivotal role in the valve manufacturing sector by automating complex and intricate processes. Robotic arms are capable of executing precise movements, such as welding, polishing, and assembly, with remarkable speed and accuracy, ensuring consistent results.
The integration of automation and robotics in valve manufacturing has also led to enhanced worker safety. Dangerous and physically demanding tasks can now be performed by robots, reducing the risk of workplace injuries and providing a safer working environment.
Additionally, automation and robotics have significantly increased the production capacity of valve manufacturers in India. The faster production cycles and increased output have helped meet growing demands, both domestically and globally.
In conclusion, the integration of automation and robotics in the Indian valve manufacturing sector has revolutionized the industry, offering improved efficiency, quality, and worker safety. Valves Manufacturers in India are leveraging these advancements to enhance their competitive edge and meet the evolving needs of the market.
Digitalization and IoT: Transforming the Landscape of Valve Manufacturing in India
Digitalization and the Internet of Things (IoT) have emerged as transformative forces in the valve manufacturing sector in India. This wave of technological innovation has revolutionized traditional manufacturing processes, improving efficiency, productivity, and overall performance. Here are some key points highlighting the impact of digitalization and IoT on valve manufacturing in India:
Connectivity and Remote Monitoring: IoT-enabled valves are equipped with sensors and communication capabilities that allow real-time monitoring and control, enabling manufacturers to remotely manage valve operations and collect valuable data.
Predictive Maintenance: IoT technology enables predictive maintenance by continuously monitoring valve performance and analyzing data to detect potential issues or failures in advance. This helps valve manufacturers in India schedule maintenance activities proactively, minimizing downtime and optimizing operational efficiency.
Enhanced Operational Efficiency: Digitalization enables automation and integration of valve systems with other manufacturing processes, resulting in streamlined operations, improved accuracy, reduced manual intervention, and increased productivity.
Data Analytics and Insights: By leveraging digitalization, valve manufacturers can collect and analyze vast amounts of data from sensors and connected devices. This data can be used to gain valuable insights into production trends, performance patterns, and customer preferences, enabling informed decision-making and driving innovation.
Improved Quality Control: Digitalization facilitates real-time quality monitoring and control throughout the valve manufacturing process, ensuring adherence to strict standards and reducing the risk of defects or failures.
Digitalization and IoT have significantly transformed the valve manufacturing landscape in India, empowering manufacturers to enhance operational efficiency, optimize maintenance practices, and deliver high-quality valves that meet the evolving needs of various industries. Valves manufacturers in India have embraced these technologies to stay competitive in the global market and provide cutting-edge solutions to their customers.
Advanced Materials and Manufacturing Techniques in the Indian Valve Industry
The Indian valve industry has witnessed remarkable advancements in materials and manufacturing techniques, enabling manufacturers to deliver high-quality valves that meet global standards. With a focus on innovation and technology, valve manufacturers in India have embraced cutting-edge practices to enhance performance, durability, and efficiency in valve production. Here are some key highlights of advanced materials and manufacturing techniques in the Indian valve industry:
Advanced materials: Valves manufacturers in India are utilizing a wide range of advanced materials to enhance valve performance. These materials include stainless steel, carbon steel, alloy steel, brass, bronze, and exotic alloys like Hastelloy and Inconel. Each material possesses specific characteristics suitable for diverse applications, ensuring optimal functionality and longevity.
Precision machining: The Indian valve industry has adopted precision machining techniques to ensure accurate dimensions, smooth surface finishes, and tight tolerances. Advanced CNC (Computer Numerical Control) machines are employed for precise shaping, drilling, and threading of valve components, ensuring consistent quality and performance.
Coating technologies: Coatings play a vital role in protecting valves from corrosion, wear, and erosion. Indian valve manufacturers are utilizing advanced coating technologies such as ceramic coatings, polymer coatings, and metal coatings to enhance the durability and lifespan of valves, especially in harsh operating environments.
Advanced casting methods: Valve manufacturers in India are employing advanced casting methods such as investment casting and sand casting to produce intricate valve components with superior strength and dimensional accuracy. These techniques enable the production of complex valve designs that meet stringent industry requirements.
Non-destructive testing (NDT): To ensure the highest quality standards, Indian valve manufacturers utilize non-destructive testing techniques such as ultrasonic testing, radiographic testing, and magnetic particle inspection. These methods allow for the detection of any defects or irregularities in valves, ensuring reliable and safe operation.
Valves manufacturers in India are continuously investing in research and development to explore new materials, refine manufacturing processes, and introduce innovative designs. By leveraging advanced materials and manufacturing techniques, the Indian valve industry is poised to meet the evolving needs of various sectors, including oil and gas, power generation, water treatment, and industrial processes. As a result, valves manufacturers in India are becoming increasingly competitive in the global market, offering high-quality valves that cater to diverse applications and provide optimal performance and reliability.
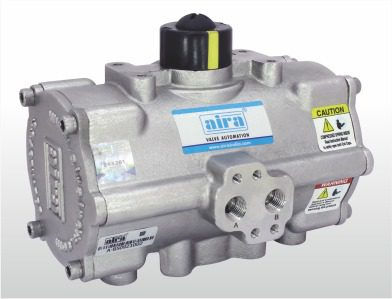
Smart Valve Technology: Enhancing Efficiency and Performance in India
In recent years, the Indian valve manufacturing industry has witnessed significant advancements with the introduction of smart valve technology. This innovative technology has revolutionized the way valves are designed, manufactured, and operated, leading to enhanced efficiency and performance in various industries. Here are some key points highlighting the impact of smart valve technology in India:
Intelligent Control: Smart valves incorporate advanced control systems that enable real-time monitoring and adjustment of valve parameters, ensuring precise and optimal operation.
Remote Monitoring: These valves are equipped with sensors and communication capabilities, allowing remote monitoring of valve conditions, performance, and health parameters.
Predictive Maintenance: Smart valves utilize data analytics and machine learning algorithms to predict maintenance needs, enabling proactive maintenance and reducing downtime.
Energy Efficiency: Smart valve technology optimizes energy consumption by efficiently regulating fluid flow and minimizing unnecessary pressure drops.
Enhanced Safety: Smart valves feature built-in safety mechanisms such as emergency shut-off, leak detection, and automatic response to critical situations.
Integration with Industrial IoT: Smart valves can seamlessly integrate with industrial IoT platforms, enabling enhanced data exchange and interoperability within the manufacturing ecosystem.
Valve manufacturers in India have embraced smart valve technology to meet the increasing demand for efficient and intelligent solutions. By leveraging these advancements, valve manufacturers in India are driving performance improvements, cost savings, and sustainable operations for industries across the country.
Innovative Design and Engineering in Indian Valve Manufacturing
Valve manufacturers in India have been at the forefront of adopting innovative design and engineering practices to meet the evolving demands of various industries. With a focus on improving performance, reliability, and efficiency, Indian valve manufacturers have incorporated cutting-edge technologies and advanced design techniques. Here are some key aspects of innovative design and engineering in the Indian valve manufacturing sector:
Advanced CAD/CAM Software: Indian valve manufacturers leverage advanced computer-aided design (CAD) and computer-aided manufacturing (CAM) software to create precise and complex valve designs. This enables them to optimize performance and reduce manufacturing costs.
Computational Fluid Dynamics (CFD) Analysis: CFD analysis plays a crucial role in valve design by simulating fluid flow patterns and identifying potential issues. Indian manufacturers utilize CFD analysis to enhance valve performance, minimize pressure drops, and improve overall efficiency.
Material Selection: Indian valve manufacturers carefully select materials based on the specific requirements of different applications. They explore innovative materials such as high-performance alloys and composite materials to enhance durability, corrosion resistance, and operational lifespan.
Ergonomic Design: Valve manufacturers in India prioritize ergonomic design to improve ease of operation and maintenance. They focus on intuitive user interfaces, accessible valve components, and optimized dimensions to enhance user experience.
By combining innovative design and engineering practices, Indian valve manufacturers are continuously pushing the boundaries of valve technology. Their commitment to research and development, coupled with a customer-centric approach, positions them as key contributors to the global valve industry.
Data Analytics and Predictive Maintenance in Indian Valve Industry
Data analytics and predictive maintenance have emerged as critical tools in the Indian valve manufacturing industry. By harnessing the power of data and advanced analytics techniques, valve manufacturers in India are enhancing their operational efficiency, reducing downtime, and optimizing maintenance practices. Here are some key aspects of data analytics and predictive maintenance in the Indian valve industry:
Data-driven decision-making: Valves manufacturers in India are leveraging data analytics to gain actionable insights into their operations. By collecting and analyzing data from various sources, such as sensors, equipment monitoring systems, and historical maintenance records, manufacturers can make informed decisions regarding maintenance schedules, asset management, and process optimization.
Predictive Maintenance: Predictive maintenance techniques are being adopted by Indian valve manufacturers to detect potential equipment failures before they occur. By analyzing real-time data and employing machine learning algorithms, manufacturers can identify patterns and indicators that signify equipment degradation or failure. This proactive approach allows for timely maintenance interventions, minimizing unplanned downtime and maximizing equipment lifespan.
Condition monitoring: Indian valve manufacturers are implementing condition monitoring systems that continuously collect and analyze data from valves and related equipment. These systems use various sensors and monitoring devices to track parameters such as temperature, pressure, vibration, and fluid flow. By monitoring these parameters in real time and comparing them against established thresholds, manufacturers can detect anomalies and take corrective actions promptly.
Remote monitoring and diagnostics: With the advancements in connectivity and the Internet of Things (IoT), Indian valve manufacturers can remotely monitor and diagnose valve performance. By leveraging IoT-enabled sensors and connectivity solutions, manufacturers can access real-time data from valves installed in diverse locations. This capability enables them to detect issues, diagnose problems remotely, and even provide predictive maintenance recommendations without the need for physical inspection.
The adoption of data analytics and predictive maintenance practices by valve manufacturers in India is revolutionizing the industry. By harnessing the power of data, these manufacturers can optimize their operations, improve reliability, and deliver better products to their customers. As the valve industry in India continues to embrace digital transformation, data analytics and predictive maintenance will play a crucial role in achieving higher efficiency, reducing costs, and ensuring customer satisfaction.
Integration of Artificial Intelligence in Valve Manufacturing: Indian Innovations
Artificial Intelligence (AI) has revolutionized various industries, and the valve manufacturing sector in India is no exception. Indian valve manufacturers have embraced AI technologies to enhance production processes, improve efficiency, and optimize performance. By leveraging AI, they have achieved remarkable advancements in valve manufacturing. Here are some key innovations and applications of AI in the valve manufacturing sector in India:
Predictive Maintenance: Indian valve manufacturers are utilizing AI-powered predictive maintenance techniques to monitor the condition of valves in real time. By analyzing data collected from sensors and historical records, AI algorithms can detect potential failures or malfunctions before they occur, enabling proactive maintenance and reducing downtime.
Quality Control and Inspection: AI-based computer vision systems are being deployed in Indian valve manufacturing units for quality control and inspection purposes. These systems can detect defects, measure dimensions accurately, and identify any deviations from the desired specifications, ensuring high-quality valves are produced.
Process Optimization: AI algorithms are employed to optimize the valve manufacturing process in India. By analyzing vast amounts of data, AI systems can identify patterns, optimize parameters, and suggest process improvements to enhance productivity, reduce waste, and minimize production costs.
Intelligent Design: Indian valve manufacturers are utilizing AI to enhance the design phase of valve production. AI algorithms can analyze performance requirements, simulate fluid dynamics, and generate optimized valve designs that maximize efficiency and meet specific operational needs.
Supply Chain Optimization: AI-based supply chain optimization tools are employed by Indian valve manufacturers to improve inventory management, demand forecasting, and logistics. By analyzing market trends, customer demands, and production capabilities, AI systems can optimize the supply chain, ensuring timely delivery of valves and reducing inventory holding costs.
These Indian innovations in integrating AI in valve manufacturing demonstrate the commitment of Indian valve manufacturers to leverage cutting-edge technologies. By harnessing the power of AI, they have enhanced the quality, efficiency, and competitiveness of valve production in India, solidifying their position as a prominent hub for valve manufacturing.
Overall, the integration of artificial intelligence in valve manufacturing has paved the way for increased automation, improved product quality, reduced costs, and optimized processes. The Indian valve manufacturers' adoption of AI technologies showcases their dedication to embracing innovation and staying at the forefront of the industry. Valves Manufacturers in India can benefit greatly from these advancements and continue to thrive in a rapidly evolving market.
Industry 4.0 and the Future of Valve Manufacturing in India
The advent of Industry 4.0, often referred to as the fourth industrial revolution, has been transforming various sectors worldwide, and the valve manufacturing industry in India is no exception. With the integration of advanced technologies, connectivity, and data-driven insights, Industry 4.0 holds tremendous potential for revolutionizing valve manufacturing processes, enhancing efficiency, and shaping the future of the industry in India.
Here are some key aspects of Industry 4.0 and its impact on the future of valve manufacturers in India:
Smart Manufacturing: Industry 4.0 brings forth the concept of smart factories, where automation, robotics, and IoT (Internet of Things) play a crucial role. Valve manufacturers in India are increasingly adopting automated systems and intelligent machinery for improved precision, productivity, and quality control.
Data-Driven Insights: The implementation of Industry 4.0 technologies enables valve manufacturers to gather real-time data from various sources, such as sensors and production equipment. Advanced analytics and machine learning algorithms help in analyzing this data, identifying patterns, and making informed decisions for optimizing production processes and minimizing downtime.
Predictive Maintenance: With the help of Industry 4.0 technologies, valve manufacturers in India can move from a reactive maintenance approach to a predictive maintenance strategy. By utilizing sensor data and predictive analytics, manufacturers can anticipate maintenance needs, detect potential failures in advance, and schedule maintenance activities proactively. This leads to reduced downtime, increased operational efficiency, and cost savings.
Supply Chain Optimization: Industry 4.0 facilitates improved communication and collaboration among stakeholders in the valve manufacturing supply chain. Through the integration of digital technologies, manufacturers can achieve real-time visibility of inventory, streamline logistics, and enhance coordination with suppliers, resulting in improved responsiveness and reduced lead times.
Skill Development and Workforce Transformation: The implementation of Industry 4.0 technologies necessitates a skilled workforce capable of operating and maintaining advanced manufacturing systems. Valve manufacturers in India are focusing on upskilling their employees and promoting a culture of continuous learning to adapt to the changing requirements of the industry.
As Industry 4.0 continues to evolve, valve manufacturers in India need to embrace these technologies and leverage their potential to stay competitive in the global market. By incorporating smart manufacturing practices, harnessing data-driven insights, and investing in skill development, the future of valve manufacturers in India holds promising prospects for growth, innovation, and efficiency.
Collaboration and R&D Initiatives: Driving Innovation in Indian Valve Sector
The Indian valve manufacturing sector has witnessed significant growth and innovation in recent years. One of the key driving factors behind this progress is the focus on collaboration and research and development (R&D) initiatives. By joining forces and fostering partnerships, valve manufacturers in India have been able to pool their resources, knowledge, and expertise, resulting in groundbreaking innovations and advancements in the industry.
Here are some key points highlighting the role of collaboration and R&D initiatives in driving innovation in the Indian valve sector:
Knowledge exchange: Collaboration and R&D initiatives provide a platform for valve manufacturers in India to share their knowledge, best practices, and technological advancements. By collaborating with industry experts, research institutions, and academic organizations, valve manufacturers can tap into a vast pool of expertise and gain valuable insights to enhance their manufacturing processes.
Research and innovation centers: Many valve manufacturers in India have established dedicated research and innovation centers to facilitate collaborative efforts. These centers serve as hubs for conducting research, developing new technologies, and testing innovative valve designs. By investing in R&D infrastructure, manufacturers can stay at the forefront of technological advancements and develop cutting-edge valves to meet industry demands.
Industry-academia partnerships: Collaboration between valve manufacturers and academic institutions plays a crucial role in driving innovation. By collaborating with universities and research institutes, manufacturers can leverage academic research and access specialized knowledge. These partnerships often result in joint R&D projects, collaborative studies, and knowledge transfer programs, fostering a culture of innovation in the Indian valve sector.
Technology transfer and licensing: Collaboration also extends to technology transfer and licensing agreements. Valve manufacturers in India actively seek partnerships with global technology leaders to acquire advanced manufacturing techniques, patents, and know-how. Such collaborations enable the transfer of state-of-the-art technologies, allowing Indian valve manufacturers to enhance their capabilities and produce high-quality valves that meet international standards.
Valve manufacturers in India recognize the importance of collaboration and R&D initiatives in driving innovation. By actively engaging in partnerships, sharing knowledge, and investing in research and development, the Indian valve sector continues to thrive and contribute to the advancement of the industry globally.
The way Indian valve manufacturers are adopting automation, IoT, and even AI is really impressive—it shows how the industry is moving toward global standards while also creating smarter and more efficient solutions. I also found it helpful to get business insights on reviews it website now, as it explains how these innovations are shaping different sectors in India.
Homework help is an essential component in the development of students' academic careers within the dynamic educational system that defines Canada. As part of their mission to produce well-rounded citizens, educational institutions and websites in Canada offer cross-disciplinary resources to assist students with their assignments. Students all around Canada have access to a multitude of tools that not only help in comprehending but also build critical thinking skills. These resources range from looking at rich literary themes to deciphering complex mathematical problems. Students are given the ability to achieve in their studies and are given a profound feeling of confidence in their academic endeavours when these support systems encourage time management, independent study, and collaborative problem-solving. In a country known…
Online coursework experts have changed academic help in the digital era. In order to succeed academically while juggling a variety of other responsibilities, students can benefit greatly from the guidance of these experts. With a wealth of knowledge and experience at their disposal, online coursework experts provide personalised guidance, ensuring a deeper understanding of subjects and improved grades. Hire Online Coursework Expert helps students learn at their own speed. Whether you are having trouble with complicated equations, analysing books, or doing science projects, these experts can help you find answers that fit your way of learning. Beyond the confines of the classroom, their perspectives provide students with useful applications and real-world experiences that complement theoretical knowledge. But it is crucial…