The Butterfly Valve With Actuator: A Comprehensive Guide
- Aira Euro Automation
- Mar 3, 2023
- 4 min read
If you're looking for information about butterfly valves with actuators, you've come to the right place. In this blog post, we'll cover everything you need to know about these valves, from their working principle and benefits, to how to choose the right one for your application. We'll also examine the different types of butterfly valves with actuators and their construction. So without further ado, let's get started!
In what way is a butterfly valve with an actuator different from a regular butterfly valve?
With a butterfly valve with actuator, fluids or gasses are controlled by a rotating disc inside the valve. The disc is mounted on a shaft that runs through the center of the valve body and is connected to an actuator (usually a motor) that controls the rotation of the disc. Butterfly valves are used in various applications, including oil and gas pipelines, water treatment plants, and HVAC systems.
Butterfly valves are often used when fluids or gasses must be controlled quickly and efficiently. For example, in an oil pipeline, if there is a sudden increase in pressure downstream of the valve, the butterfly valve can be quickly opened to release the tension and prevent damage to the pipeline. Similarly, butterfly valves can control the flow of treated water into and out of storage tanks in a water treatment plant.
Butterfly valves can also be used in HVAC systems to control airflow through ducts. In this application, butterfly valves are often used in conjunction with damper actuators, which contain the position of the damper (a movable plate that regulates airflow). By controlling both the part of the damper and the flow rate through the butterfly valve, HVAC engineers can precisely control airflow throughout a building.
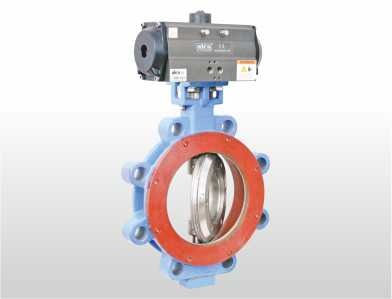
The working principle of a butterfly valve with an actuator
A butterfly with an actuator is a quarter-turn valve with a disk-shaped closure element to control fluid flow through a pipe. The disk is connected to a shaft rotated by an actuator, and as the post is turned, the disk opens or closes the valve. Butterfly valves are named after their similarity to a butterfly's wings. They are often used in applications requiring high flow control, such as in water treatment plants or oil refineries.
The working principle of a butterfly valve with an actuator is relatively simple; when the actuator is turned in one direction, the disk rotates and opens the valve, allowing fluid to flow through. When the actuator is turned in the other direction, the disk closes and blocks the fluid flow. The amount of rotation required to open or close the valve can be adjusted by changing the position of the stop pins on the actuator, which limits the travel of the shaft and, therefore, the opening or closing of the valve.
Butterfly valves with actuators are well-suited for use in applications with limited space, as they are compact and require less installation space than other valves. They are also relatively easy to maintain and repair and can be operated manually in emergencies if power is lost.
The benefits of butterfly valves with actuators
Butterfly valves with actuators offer several advantages over other valves, making them an ideal choice for many applications. Due to their simple design, they are much easier to install and maintain than other valves. Butterfly valves with actuators also have a much higher flow capacity than different types of valves, making them an ideal choice for applications where a large volume of fluid needs to be moved quickly. Additionally, butterfly valves with actuators are much more versatile than other valves and can be used in various applications.
How to choose the suitable butterfly valve with an actuator for your application
When choosing a butterfly valve with an actuator, it is essential to consider the specific needs of your application. The first step is determining the maximum flow rate required for your application. This will help you to choose a valve with the appropriate size and capacity for your needs. It is also essential to consider the pressure that will be present in the system, as this will affect the choice of materials and construction of the valve. Additionally, it is essential to ensure that the actuator chosen is compatible with the control system used to operate it.
The different types of butterfly valves with actuators
Several different butterfly valves have actuators, each designed for specific applications. The most common type is the wafer butterfly valve, intended for use between two flat surfaces, such as two pipes. These valves are easy to install and maintain and offer a high flow capacity. Another common type is the lug butterfly valve, designed for use in limited space applications. These valves provide a compact design and are easy to install and maintain. Finally, the flange butterfly valve is designed for use in applications with high pressure. These valves offer a robust design and can handle high pressures.
The construction of butterfly valves with actuators
Butterfly valves with actuators are typically made from one of two materials: metal or plastic. Metal butterfly valves are more common in high-pressure applications, while plastic butterfly valves are more common in low-pressure applications. The most common type of metal used in constructing butterfly valves is stainless steel due to its high corrosion resistance. Plastic butterfly valves are typically made from polypropylene or PVC, offering good chemical resistance and weathering resistance.
The body of the butterfly valve is typically made from cast iron, ductile iron, or cast steel. The disk is also typically made from one of these materials, although some manufacturers offer stainless steel or aluminum disks. The seat is usually made from a soft material such as rubber or synthetic polymer, which provides a seal between the disk and the valve's body. The actuator is typically made from aluminum, although some manufacturers also offer stainless steel or plastic actuators.
When choosing a butterfly valve with an actuator, it is essential to consider the specific needs of your application. The first step is determining the maximum flow rate required for your application. Additionally, it is necessary to consider the pressure that will be present in the system, as this will affect the choice of materials and construction of the valve. Additionally, it is essential to ensure that the actuator chosen is compatible with the control system used to operate it.
Comentarios