The Different Types Of Non Returning Valves And Their Benefits
- Aira Euro Automation
- Mar 24, 2023
- 8 min read
Non-return valves are a critical component in many industrial and commercial applications. They are designed to prevent the reverse flow of liquids and gasses and can be used in various ways. This blog post will discuss the different types of non-return valves, their benefits, and how to choose the right one for your application. We will also provide instructions on how to install a non-return valve. With this information, you can decide on the best type of valve for your needs.
Introduction
The Different Types Of Non-Return Valves And Their Benefits
Non-return valves (NRV) are integral to many piping systems, controlling the flow of fluids and glasses. This type of valve is used in a wide range of industries, from plumbing to automotive engineering to industrial processes. They are designed to prevent backflow, maintain pressure or vacuum within a system, and protect against contamination. NRVs come in various sizes, shapes, and materials to meet the requirements of different applications. In this article, we will look at the different types of non-return valves and their benefits.
The most common type of NRV is the plunger valve, which consists of a cylindrical body with an internal plunger that can be opened or closed depending on the direction of flow. The plunger valve is easy to operate and maintain, making it ideal for residential and commercial buildings. It has good sealing capabilities and can be used for water systems up to several hundred pounds per square inch (PSI).
Another type of NRV is the swing check valve, which features a disc inside the cylinder that swings open when pressure from upstream causes it to move outwards. When no pressure is present, gravity will cause the disc to close shut again automatically. These valves are often used for large pipeline applications with higher pressures and require less maintenance than other valves.
Ball check valves feature a spherical ball mounted inside a chamber with two outlets; one outlet allows fluid flow while the other prevents reverse flow when closed off by the ball. These valves are usually made from stainless steel or brass and have excellent sealing capabilities even at high pressures of up to 600 PSI. Ball check valves are usually installed horizontally with their outlet facing downwards to ensure proper functioning without any leakage or noise issues.
Butterfly check valves also feature discs that move when pressured by upstream flows. Still, they also have additional flaps that help direct flow more efficiently when open or closed off completely when there's no upstream pressure present. Butterfly valves offer excellent performance at lower pressures, up to 150 PSI but require more frequent maintenance due to their design complexity compared with other NRV types.
Finally, diaphragm check valves use rubber membranes instead of discs or balls for operation; these membranes flex outward under pressure from upstream flows, allowing them through while preventing backflow when not pressurized anymore thanks to their elasticity properties, keeping them shut tight again afterward. Diaphragm check valves can be used for processes involving corrosive substances, making them ideal for chemical plants or wastewater treatment facilities where such substances may be handled regularly, requiring special protection against backflows into sensitive equipment downstream, such as pumps or compressors, among others.
What are the different types of non-return valves?
Non-return valves, also known as check valves, are mechanical devices that allow the flow of liquid or gas in one direction while preventing the backflow of liquid or gas in the opposite direction. These valves are typically used to ensure the safety and integrity of a system's pressure levels and prevent contamination from backflow. Non-return valves can be classified into several types based on design, functionality, and applications.
The most common type is a swing check valve. This valve consists of a disc connected to a hinged arm held against the valve seat by gravity or spring tension. When fluid flows through the valve in the proper direction, it lifts the disc off its seat and allows passage through the valve. However, when fluid flows in the opposite direction, gravity or spring tension causes the disc to close against its seat and prevent backflow. Swing check valves are typically used when an instant pressure surge is caused by upstream pumps or other sudden pressure changes that could damage downstream equipment if not checked properly.
Another type of non-return valve is a lift check valve. In this design, instead of relying on gravity or springs to keep it closed when reversed flow occurs, an internal mechanism opens and closes based on pressure differences between two points on either side of the valve body. Lift check valves also feature a flap-like disc that partially lifts off its seat when forward flow occurs but completely seals shut when reverse flow occurs due to increased pressure on one side of the body relative to another side. They are commonly used for applications where reverse flow should never occur regardless of any change in upstream pressures, such as sewerage systems and water supply lines where contamination must always be prevented.
A third type of non-return valve is a ball check valve which uses a spherical ball inside its body instead of discs like with other designs mentioned above. This ball operates similarly to discs in that it allows forward flow but prevents backflow due to higher pressures on one side compared to another; however, since it has no moving parts like discs do, it requires less maintenance overall than other types making it quite popular for many industrial applications such as oil pipelines and chemical processes where reliability is critical over long periods without service interruptions due to worn out parts.
Finally, there are dual plate check valves which rely on two plates instead of discs or balls for their operation; these plates open up when forward flow occurs, allowing passage but close tightly shut against each other when reverse flow begins due to higher pressures on one side compared to the other thus preventing any further backflow from occurring further downstream within a system. Dual plate check valves are often preferred for high velocity systems due to their unique construction, which allows them more excellent resistance towards wear from flowing particles mixed within fluids passing through them than other designs have historically been able to offer until recently with newer developments such as Hard-Wearing Ball Check Valves (HBCV).
The benefits of using a non-return valve
Using a non-return valve offers numerous benefits to both industrial and residential applications. One of the primary advantages is that it helps protect against backflow, which can be especially dangerous in specific systems. Backflow can cause contamination from unwanted materials, leading to serious health risks if it reaches drinking water. Non-return valves also help maintain consistent pressure levels within the system, ensuring proper operation and preventing damage due to overpressure or under pressure conditions.
Non-return valves are also highly reliable since they have few moving parts; this reduces maintenance costs and increases their lifespan. Being so reliable also means that they work effectively when needed, providing peace of mind that your system is always protected. Additionally, since they don't rely on human interaction for operation, non-return valves are ideal for automated systems where human intervention would be difficult or impossible.
Finally, the non returning valve can provide significant cost savings over time due to their low maintenance requirements and long life span. Since there are so few parts in a non-return valve that need replacing or repairing compared to other valves, you will save money on parts and labor costs associated with regular maintenance checks. This allows businesses to maximize their return on investment by reducing costly downtime caused by faulty equipment or inefficient operations.
Which type of valve is right for my application?
When it comes to choosing the right type of non-return valve for an application, several factors need to be taken into consideration. The first and most important is the pressure rating of the valve. This pressure rating indicates the maximum amount of pressure that can be used with the valve before it fails or begins to leak. Depending on the system and application, this rating will help dictate which type of valve should be used.
The next factor to consider is compatibility with other components in the system. Swing check valves may not be suitable for systems with high flow rates, as they are designed primarily for low-velocity applications. Lift check valves require more maintenance than ball check valves, so if maintenance requirements are an issue, then ball check valves may be better suited for that application. Dual plate check valves offer superior durability and reliability in high velocity systems but also come with a higher price tag and require more space than other types of non-return valves.
Other considerations include cost, size constraints, corrosion resistance needs, sealing requirements, and more, depending on the specific application's needs. Consultation with an expert or experienced technician can help customers decide which type of valve best suits their system and application needs.
Ultimately when selecting a non-return valve, it is essential to consider all aspects mentioned above before making a final decision. Both short-term costs and long term benefits should play a role in determining which type of valve best suits your specific application needs.
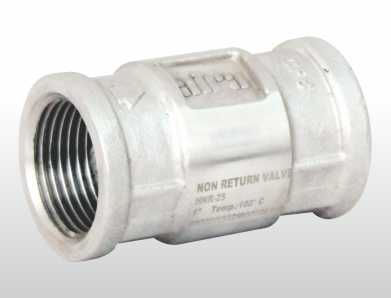
How to install a non-return valve
Installing a non-return valve is an essential step in ensuring the safety and functionality of a system. This type of valve requires special attention during installation to ensure it functions properly. Here are some guidelines on how to install a non-return valve:
1. Begin by selecting the proper type of non-return valve for your application. Consider factors such as pressure rating, compatibility with other components, cost, size constraints, corrosion resistance needs, sealing requirements, and more. Consulting an expert or experienced technician can help guide customers to the correct type of valve for their application needs.
2. Once you have chosen the correct non-return valve for your system, test and fit it into its location to ensure it fits correctly and can operate correctly when installed. Ensure that the flange holes' orientation aligns correctly with those on the pipe or other connection point to fit correctly when bolted together later.
3. When installing a non-return valve, make sure that you apply appropriate tightening torque when bolting it in place; otherwise, it may not operate as intended due to leakage between connections or through fittings which could lead to contamination or other problems within your system. You should also check for any obstructions caused by incorrect installation or debris that might prevent the valve from fully opening or closing completely when needed.
4. It's essential to check for leaks around the connections where your non-return valves were installed before use; this is best done using a pressure gauge connected directly to one end of each connection point while running water through all points until all connections are dry (or at least no more than 5% wet). Suppose any leaking occurs at any point during testing. Further tightening may be necessary until all connections are sealed securely, and no leaks are present before safely putting your system into operation.
5. Finally, after following these steps and confirming that your non-return valves have been successfully installed and tested according to manufacturer recommendations, you can put your system back into operation safely, knowing that you have taken all necessary precautions against potential damage due to backflow contamination or pressure surges due to improper installation methods and techniques used during set up procedures earlier on in this process!
Conclusion
Non-return valves are an essential component of many systems, offering a range of benefits such as reliable pressure levels, protection against backflow, cost savings, and low maintenance requirements. Different types of non-return valves offer varying advantages and disadvantages depending on the application needs – it is essential to consult an expert or experienced technician when selecting the right type for your system. The installation process should also be conducted carefully to ensure a successful outcome. Considering all these factors will help ensure that your system is safe and functioning at its highest level of efficiency.
Thank you for sharing this article. Hey, I'm Mac Davis, a technical support specialist, and I can assist you with the QuickBooks Migration Failed Unexpectedly. With my skills, I can quickly resolve any issues related to it, ensuring uninterrupted communications for individuals and businesses.